Repair Tank 156 and 105
Description
Bristol was awarded this fuels project to inspect, repair, cut, and cover Tanks 105 and 156 at Naval Station Guantanamo Bay to bring them into compliance with the applicable API 653 and to extend the life of the tanks. Repairs included repairing non-compliant welds, sealing roof welds, installing stilling wells, replacing threaded piping with welded fittings, recoating the interior of the tank, and placing a liner over the roof of the tank.
Bristol conducted an onsite repair validation to include verification and validation of the repairs listed in the scope of work. A report was submitted to the client listing all current repairs and included repairs no longer needed as well as repairs that must be added to this scope of work for both Tank 156 and Tank 105. Additional repairs identified included replacement of a non-compliant ladder, testing of 11 existing patch plate welds to determine if they were in compliance, installation of product recovery tanks, removal of salt contamination from interior tank steel, as well as installation of a liner over the tank roof and under the soil to prevent water from entering the tank.
Tank 156 is a Cut and Cover JP-5 underground storage tank (UST). The tank’s dimensions are 20 feet (ft) high by 100 ft deep, with a barrel size of 27,900 barrels. Bristol performed an American Petroleum Institute (API) 653 Modified inspection as well as other repairs to extend the life of the tank, including the removal of 25,000 square feet (SF) of existing coating system and provided a new coating system on the roof, floor and shell. The initial coating removal was completed by abrasive blasting steel surfaces to near-white metal IAW SSPC SP-10/NACE No. 2. Once the existing coating was removed, the underlying steel was found to contain gross contamination from salt. Once removal of the salt contamination was complete, the tank was coated by applying a three-coat system IAW UFGS 09 97 13.17, Three Coat Epoxy Interior Coating of Welded Steel Petroleum Fuel Tanks.
Bristol provided seal welds for any incomplete welds including the entire 315 linear feet (LF) inner circumferential joint at the tank shell and rim angle as this joint may be a potential leak path in the future. Back welded all plate joints (1,750 LF) to prevent future leak paths.
For UST 105 Bristol provided 1,990 SF of internal coating repair on the tank bottom (mainly under the manway opening), along the tank sump and secondary sump bottoms, and 100 SF of internal coating on the steel roof deck. All surfaces were abrasive blasted and received three coats of interior coating to the same specifications used on Tank 156.
Due to the remote nature of this site, Bristol constructed a fully self-contained man camp to provide housing and facilities for construction staff performing the cleaning, inspection, and repair of these tanks. Bristol shipped all material and equipment from the mainland to the site on a government-contracted barge.
Repair Tank 156 and 105
Client: 772D Enterprise Sourcing Squad
Location: Cuba
contract amount: $7.5 million
Award Date: March 2016
Highlights
- Remote and logistically challenging site
- Man camps were constructed to provide housing and facilities for construction staff
- Repaired over 26,000 SF of existing coating systems of tanks 105 and 156
- Completed seal welds of tanks
- Man camps withstood hurricane
Highlights
- Remote and logistically challenging site
- Man camps were constructed to provide housing and facilities for construction staff
- Repaired over 26,000 SF of existing coating systems of tanks 105 and 156
- Completed seal welds of tanks
- Man camps withstood hurricane
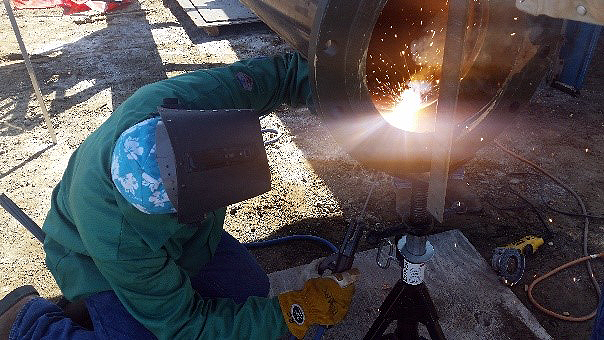
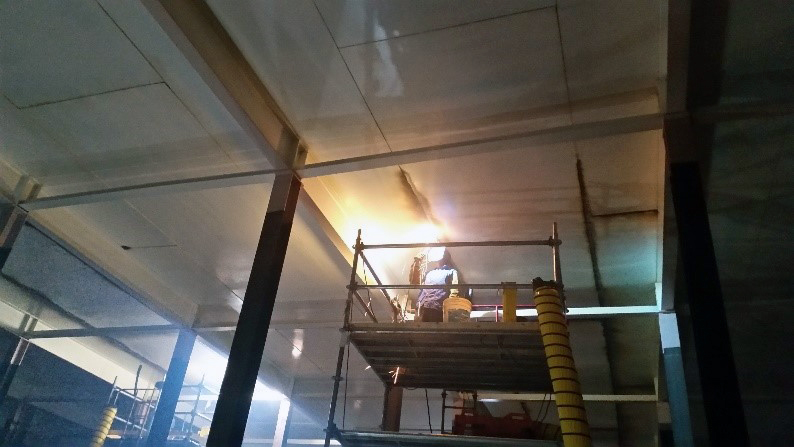
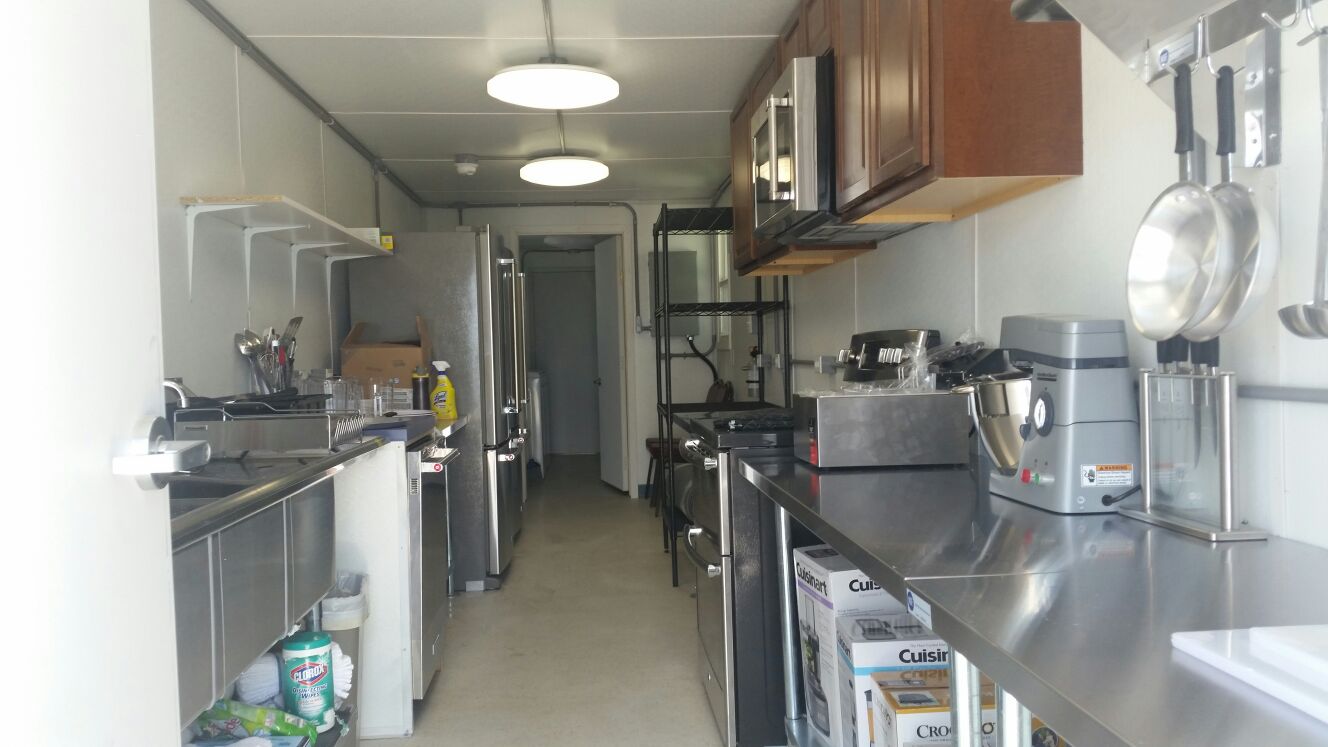